The increasing number of electronic devices in modern automobiles has increasingly required good design to meet the requirements of major electromagnetic compatibility standards. At the same time, increasing integration has made automotive designers increasingly in need of system-on-chip ASICs and proprietary standard product solutions that can replace multiple discrete components. This article explores some of the electromagnetic compatibility and integrated circuit (IC) issues faced by automotive designers.
Electronic devices in modern cars are evolving with continued momentum – engineers are developing increasingly complex solutions for automotive comfort, safety, entertainment, powertrain, engine management, stability and control applications. Moreover, advanced electronic devices are becoming more and more popular. As a result, even the most common cars today are equipped with electronic devices that were only proprietary to high-end cars a few years ago.
In the past, non-critical applications such as comfort and convenience have facilitated the development of automotive electronics applications. Like power windows or central locking, these electronic applications simply replace existing mechanical systems. Recently, the range of automotive electronics has expanded to support critical applications such as engine optimization, active and passive safety systems, and advanced infotainment systems including global positioning systems.
We are currently entering the third phase of automotive electronics development. At this stage, electronic devices not only support critical functions, but also control these key functions—whether providing important driver information and controlling the engine, as well as anti-collision detection and prevention, line control and driving. Intelligent climate control, etc. As you might imagine, these applications require low-cost, easy-to-install, and intelligent and stable electronic solutions.
Speed ​​and cost factors have contributed to the birth of the "universal" embedded hardware electronic platform. These platforms provide basic or common hardware functionality, and can be customized to provide the functionality needed for different models in the same automotive range, or even to different automotive manufacturers. System-on-a-chip (SoC) semiconductor solutions integrate multiple functions into one integrated circuit, which reduces component count and space requirements while ensuring long-term reliability, which is critical to the development of a successful general-purpose embedded electronic platform.
Electromagnetic compatibilityWith the increasing number of automotive electronic devices and the increasing use of complex electronic modules in various parts of automobiles, electromagnetic compatibility issues are becoming more and more a design challenge for engineers. Three of the main issues are:
(a) How to minimize electromagnetic sensitivity so that electronic equipment is not affected by electromagnetic emissions from other electronic systems such as cell phones, global positioning systems or infotainment equipment.
(b) How to protect electronic equipment from harsh automotive environments, including transients in power supply systems and interference from large or inductive loads such as switching lights and starter motors.
(c) How to minimize electromagnetic emissions that can affect other automotive electronic circuits.
Moreover, these problems become more and more challenging as system voltages increase, vehicle electronics increase, and the frequency of more high-frequency electronic devices rises. In addition, many electronic modules now interface with low-power, inexpensive sensors with poor linearity and zero-point offset. These sensors rely on small signals, and electromagnetic interference will be catastrophic for their normal operation.
Compatibility testing, pre-compatibility testing, and standardsThese problems mean that automotive electromagnetic compatibility testing has become an essential element of automotive design. Compatibility testing has been standardized among automakers, their suppliers and various legislative bodies. The later the electromagnetic compatibility problem is discovered, the harder it is to identify the root cause and the solution may be more limited and expensive. Therefore, considering electromagnetic compatibility issues at all stages of the process is a fundamental practice—from integrated circuit design and printed circuit board layout to module installation and final automotive layout design. To simplify this process, pre-compatibility testing that considers electromagnetic compatibility issues at the module and integrated circuit stages has been standardized.
Design integrated circuits and modules that meet electromagnetic compatibility requirementsFor integrated circuits, there are three main electromagnetic compatibility standards: Electromagnetic emission standard - IEC 61967: Measurement of radiation and conductive electromagnetic emission electromagnetic sensitivity standards in the range of 150 kHz to 1 GHz - IEC 62132: Measurement 150 thousand Electromagnetic immunity to transients in the range of 1 GHz - ISO 7637: Electrical interference caused by the conduction and coupling of road vehicles.
So how do system designers ensure that their system chips and final modules meet the above criteria? Traditional SPICE models and the like are useless at this time because the electromagnetic field is not compatible with the SPICE simulation environment. Because the size of the chip and the entire assembly is much smaller than the wavelength of the electromagnetic signal (30 centimeters at 1 GHz, much larger than the integrated circuit size), at the integrated circuit level, it is sufficiently accurate that the electromagnetic field is modeled using only the electric field. It is worth noting that radiated emissions and sensitivity are not a major issue for integrated circuits; the main issues are conducted emissions and sensitivity to effective antennas on printed circuit boards and harnesses.
Several techniques are used to ensure that electromagnetic compatibility is met, and we will look at the two issues of electromagnetic emissions and electromagnetic sensitivity one by one.
Electromagnetic emissionElectromagnetic emissions are generated by high frequency currents in the outer loop that acts as an antenna. Sources of these high-frequency currents include flipping of core digital logic such as digital signal processing and clock drivers (synchronous logic produces large, sharp current peaks with large amounts of high-frequency components), analog circuit actions, and switching digital inputs. / Output pins and high power output drivers that provide high current peaks for printed circuit boards and harnesses. To minimize the effects of these factors, designers should use low-power circuits wherever possible, which may include architectures that reduce or use adaptive supply voltages or distribute clock signals throughout the frequency domain. The number of switching elements in one clock cycle can also be reduced by turning off unused portions of the digital system. In addition, controlling the slope of the rising and falling edges of the clock and driver signals to slow the edges of the switch and provide soft switching characteristics also helps to reduce electromagnetic emissions. Finally, designers should also carefully study the external and chip layout methods. For example, a differential output signal using a "twisted pair" line produces less electromagnetic emissions and is less sensitive to electromagnetic emissions. Ensuring that the power supply and ground are close to each other and using high-efficiency power supply decoupling is also an easy way to reduce electromagnetic emissions.
Electromagnetic sensitivityRectification/pumping, parasitic devices, current and power consumption are the three most severe interference effects of low electromagnetic sensitivity. The high frequency electromagnetic power is partially absorbed by the integrated circuit and can cause some interference, including outputting high frequency high voltage to the high impedance node and high frequency large current to the low impedance node.
An important way to minimize the effects of electromagnetic susceptibility is to make the circuit symmetrical, thus avoiding the possibility of rectification. The method is to use a differential circuit topology and layout. Even if small signals are required in applications (such as the use of sensors), the topology that can handle larger common-mode signals can help the system remain linear in the case of a wide range of electromagnetic signals. Limiting the frequency input range of sensitive devices by filtering is another method that is often used, especially with on-chip filters. The high Common Mode Rejection Ratio (CMRR) and Power Supply Rejection Ratio (PSRR) design also allows the circuit to avoid rectification, reducing internal node impedance and placing all sensitive nodes on the chip. Finally, in order to avoid or control parasitic devices and currents, it is important to use protection devices to limit the level of electromagnetic sensitivity suppression. This helps to avoid rectification and keep the signal level in a symmetrical state. It is also important to minimize the substrate current and drain the current at critical locations.
12V
Dc Motor Can drive under the rated voltage 12 v dc motor, most of the products our company can achieve the 12 v voltage drive, speed can be customized according to customer demand.
Characteristics: 12V dc
motor With torque, low noise, small size, light weight, easy to use, constant speed operation, etc, also can match all kinds of reducer in order to achieve the purpose of changing the output speed and torque
Application field: 12V Dc Motor part of the armature iron core, armature, commutator and other devices, dc motor is suitable for most of the electronic products, such as electric toothbrush, razor, medical apparatus and instruments, breeze machine, mixer, etc
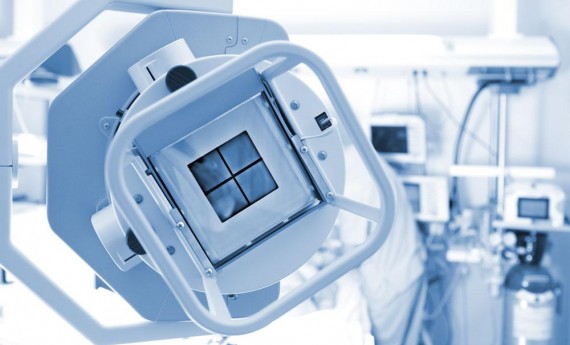
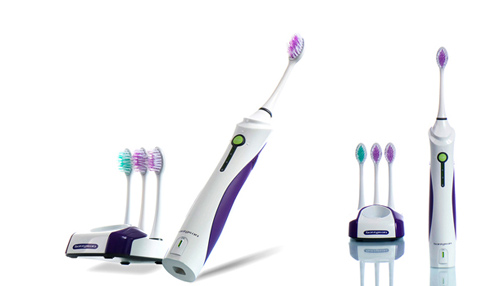
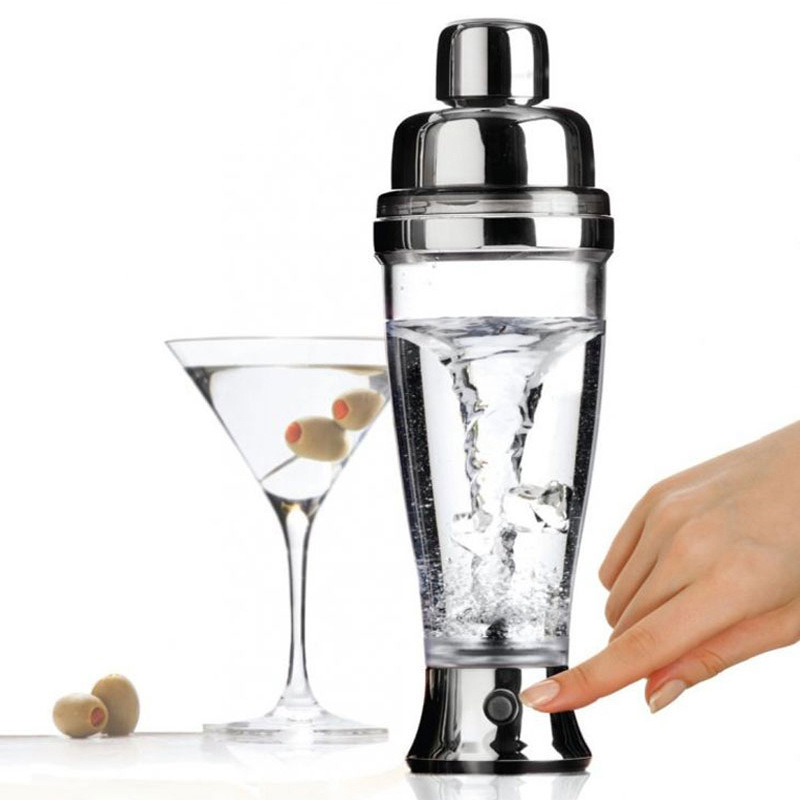
Method of use: the best stable in horizontal plane, installed on the 12V dc motor output shaft parts, cannot use a hammer to knock, knock prone to press into the 12V dc motor drive, may cause damage to internal components, and cannot be used in the case of blocked.
Operating temperature range:
12V dc motor should be used at a temperature of -10~60℃.
The figures stated in the catalog specifications are based on use at ordinary room temperature catalog specifications re based on use at ordinary room temperature (approximately20~25℃.
If a 12V dc motor is used outside the prescribed temperature range,the grease on the gearhead area will become unable to function normally and the motor will become unable to start.Depending on the temperature conditions ,it may be possible to deal with them by changing the grease of the motor's parts.Please feel free to consult with us about this.
Storage temperature range:
12V dc motor should be stored ta a temperature of -15~65℃.
In case of storage outside this range,the grease on the gearhead area will become unable to function normally and the motor will become unable to start.
Service life:
The longevity of geared motors is greatly affected by the load conditions , the mode of operation,the environment of use ,etc.Therefore,it is necessary to check the conditions under which the product will actually be used .The following conditions will have a negative effect on longevity.Please consult with us should any of them apply.
â—Use with a load that exceeds the rated torque
â—Frequent starting
â—Momentary reversals of turning direction
â—Impact loads
â—Long-term continuous operation
â—Forced turning using the output shaft
â—Use in which the permitted overhang load or the permitted thrust load is exceeded
â—A pulse drive ,e.g.,a short break,counter electromotive force,PWM control
â—Use of a voltage that is nonstandard as regards the rated voltage
â—Use outside the prescribed temperature or relative-humidity range,or in a special environment.
â—Please consult with us about these or any other conditions of use that may apply,so that we can be sure that you select the most appropriate model.
when it come to volume production,we're a major player as well .each month,we rurn out 600000 units,all of which are compliant with the rohs directive.Have any questions or special needed, please contact us, we have the engineer group and best sales department to service to you Looking forward to your inquiry. Welcome to our factory.
12V Dc Motor,Dc Motor 12V,12 Volt Dc Motor,Low Rpm Dc Motor
Shenzhen Shunchang Motor Co., LTD. , https://www.scgearmotor.com